2020年马上临近,在2019年,化工行业经历了极为不平凡的一年,化工行业的安全事故层出不穷,给整个行业拉响了沉重的警报,2019甚至被戏称为化工行业的“本命年”。无论行业的经济运行还是安全环保形势,都面临严峻的挑战,同时也承受着巨大的舆论压力。
- 3月21日14时48分许,江苏省盐城市响水县生态化工园区的天嘉宜化工有限公司发生特别重大爆炸事故,造成78人死亡、76人重伤,640人住院治疗,直接经济损失19.86亿元。11月15日,应急管理部发布事故调查报告,对44名涉案人员立案侦查并采取刑事强制措施,对涉嫌违纪违法问题的61名公职人员严肃问责。事故发生后,响水化工园区被彻底关闭,江苏省化工行业的整治提升方案出台。江苏省委办公厅下发《江苏省化工产业安全环保整治提升方案》,提出全省要大幅压减沿江地区化工企业数量,取消部分化工园区定位,压减化工园区数量等举措。而后,山东、浙江等多地也出台了化工行业的整治提升方案,对于本地区的化工企业数量和园区规范等做出了详细的要求。
- 4月24日2时34分,位于乌兰察布市卓资县旗下营工业园区的内蒙古伊东集团东兴化工有限责任公司氯乙烯气柜泄漏扩散至电石冷却车间,遇火源发生燃爆,造成4人死亡、3人重伤、33人轻伤,直接经济损失4154万元。
- 2019年7月19日17时45分左右,河南省三门峡市河南煤气集团义马气化厂C套空气分离装置发生爆炸事故,造成15人死亡、16人重伤。事故直接原因是空气分离装置冷箱泄漏未及时处理,发生“砂爆”(空分冷箱发生漏液,保温层珠光砂内就会存有大量低温液体,当低温液体急剧蒸发时冷箱外壳被撑裂,气体夹带珠光砂大量喷出的现象),进而引发冷箱倒塌,导致附近500m^3液氧贮槽破裂,大量液氧迅速外泄,周围可燃物在液氧或富氧条件下发生爆炸、燃烧,造成周边人员大量伤亡。
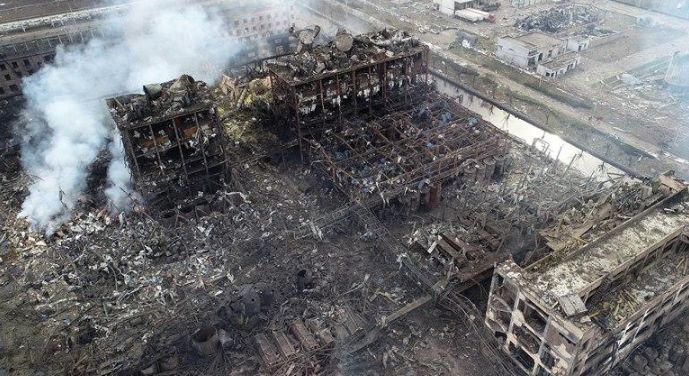
这些血淋淋的数字背后,给化工行业敲响了警钟。2019年对于化工行业来说注定是不平凡的一年,频发的事故不仅给企业带来了毁灭性的经济损失甚至是停产停业,也给伤亡者和家属带来无可挽回的人身伤害和心理阴影,更给社会造成了极为不良的影响。
事故暴露出化工企业在以下几个方面存在重大隐患:
一、人员的专业资质和综合素质
化工企业里经常会提到一句宣传口号“安全责任落实到人”。不同岗位的工作人员,对自己岗位的危险性和安全责任,都应做到心中有数、应对有方。具体来说,要具备以下能力:
1)对危险源的识别能力
哪些化工材料对人体有毒有害、哪些化工材料易燃易爆、化工装置哪些部位容易发生化工材料的泄露,都需要正确识别。
2)对事故危险性质的正确认知
许多现场人员对风险多大并没有足够的认知,比如化工材料包装袋、输送管道、储存设备一旦发生泄露,会分别产生怎样严重的后果,影响范围有多大,会造成多少人员伤亡和直接经济损失。
3)风险识别能力
如果相关工作人员没有经过正规的培训、考核就贸然上岗,则会在此方面能力不足,例如无法识别现场化工材料是否发生泄露,动火作业是否存在火灾隐患,材料存储是否按其有毒有害、易燃易爆、需防风避水等特性分区存储。
4)风险控制能力
举个例子:对危险性更大的化工设备和材料进行分区布置,加大安全保障设施的成本投资,提高管理意识、增加巡查频率,细化事故发生后的紧急处理程序等。
为了辅助和监督生产企业的工作人员合格上岗,以上这些内容,在我国现有的法律、法规之下,都有具体的行政主管部门、按时更新的技术规范、职业培训和考核机构做相关工作。
按照技术规范的要求,在应该设置可燃气体报警仪的生产部位,是否已经设置了?报警仪的工作状态是否正常,在工厂的控制系统上能否有效报警?报警信号出现以后,现场工人能否及时按操作规程处理报警情况,避免引发火情、爆炸?
二、生产设备和化工原料的品质
1)化工原料的品质
为了抑制某些化工材料的危险性,我们会对其纯度、湿度、浓度有一定的控制,或者直接为其加入一定量的抑爆剂、脱氧剂,采用高安全标准的包装和运输方式,严控存储过程中发生变质现象。
如果生产企业没有严控化工材料的采购和存储环节,从而使低品质的材料进入高温、高压的生产环境,就是埋下了巨大的安全隐患。
2)设备、管道材质选用和安装质量
大量的化工危险品具有有毒有害、易燃易爆、易腐蚀、易挥发的特性。如果生产设备和管道的材质不具备相应的耐腐蚀、防火防爆、耐高温、抗震等特性,或者安装质量不达标,那么就容易发生上述通报中的“跑、冒、滴、漏”等小问题。这跑、冒、滴、漏的,可能是水,也可能是易燃易爆、有毒的化工原料,很可能最终酿成巨大的安全生产事故。
三、生产工艺和事故处理方法
1)各工艺点的设置和监测
在化工生产过程中,存在一些重要的工艺节点,例如,原料汽化过热、高温反应、多级增压,变压吸附和分离等。为了保障产品品质和生产安全,我们需要对这些生产环节设置合理的工艺参数。为了将物料的温度、压力、流量、纯度等把控在一定的数值范围内,就要对其进行实时、有效地监测和调整。
2)事故处理方法
每一套具有危险性质的化工生产装置,在正式投产之前,都有一份用于指导生产操作的文件,相关工作人员应经过学习和考核,方能正式上岗。这份文件,通常叫做安全生产操作规程 ,由生产装置的设计方提供。其中涵括,在工艺流程中出现的各种紧急情况应该如何应对。
例如:物料反应温度过高,该怎样降温;物料反应压力过大,该通过哪些阀门和管道泄放;物料纯度不够,是再次提纯、还是直接排放以避免进入后续生产环节。
四、专业安全设施的设置
一个大型化工厂,在建厂和投产之前,要先通过专业的安全评价行政程序。在安全评价过程中,经过“定性分析”,分析含有多个危险源。再经过“定量分析”,计算多个危险源可以综合为一个“重大危险源”。“重大危险源”一旦发生安全事故,会给本厂、乃至周边地理区域,带来巨大的人员伤亡和经济损失,还可能对环境造成严重的长期影响。
根据我国现行法律法规,要求石油化工类企业,在新建项目时,将不少于5%总投资的费用,用于安全设施的设置。企业投产以后,每年仍需投入一定量的经费用作安全设施的维护。
综上所述,大多是设备老化、检查不到位,人员操作不当等可控原因。除此之外,部分地区监管部门重点工作落实不到位,安全红线意识不强,源头准入把关不严等也间接推动了事故的发生。思想松懈,心存侥幸,认为大家都是如此也就不会出事故,每次都是这样就一定没问题,敷衍了事,麻痹大意,对于事故和安全的重视程度不够,这些都是万万要不得的。
在岁末年初之际,更是化工、危化品事故高发多发时段,事故暴露出事发企业安全意识淡薄,没有认真吸取同类事故教训,管理失控,应急能力严重不足等突出问题。在此提醒各大企业,化工企业的安全规范、安全操作,一直是重中之重,安全不仅仅是一句标语,更应该落实在行动中。做到防患于未然,把风险扼杀在摇篮里,认真搞好安全工作,才是对自己负责、对企业负责、对社会负责的表现。
本文链接: https://ehsinfo.cn/posts/8e47c6d7c3e8/
版权声明: 转载请注明出处(必须保留作者署名及链接)